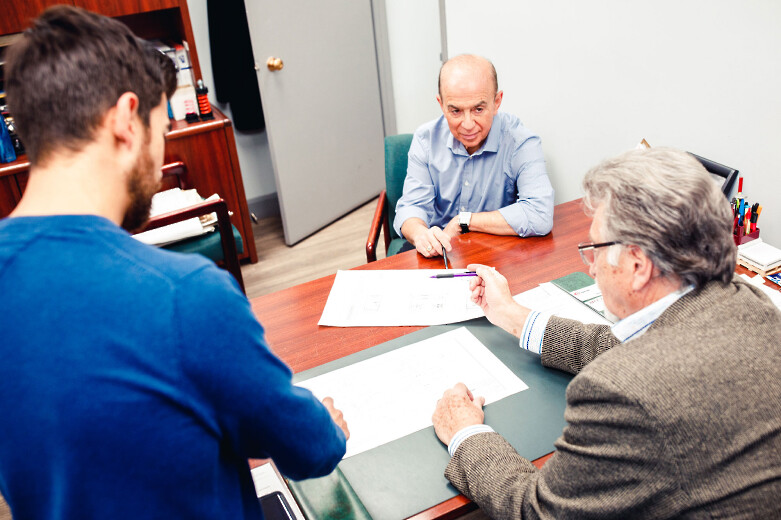
What is Vibration - Overview.
What is Vibration in simple terms- Introduction.
All of the machines used today, in both industrial and consumer environments, convert energy from one form to another. Many convert potential energy (in the form of chemical, electrical or even mechanical energy) into kinetic energy (think about a bicycle, an automobile, an electric drill, a sewing machine, a washing machine, etc.) while some machines do the opposite and convert kinetic energy (like the wind) into potential energy (e.g. a wind turbine generating electricity.)
Regardless, the conversion of one type of energy into another often involves mechanical motion. This motion can be linear or rotational.
Inevitably, some of the energy used in these machines is lost to the environment. This lost energy predominately occurs as heat, but can also occur as an oscillating motion. If this oscillating energy travels through the structure, it is called vibration. If it travels through the air, it is called sound.
The effects of sound and vibration can range from a minor customer annoyance to a loss of precision, a loss of function, accelerated wear and tear and even a catastrophic failure.
Vibration is typically a concern below 100 Hz and vibrations below 20 Hz can be especially destructive and difficult to manage. There are several strategies that can be used to address these vibrations which will be discussed in future articles.
Sound in and of itself is not a bad thing. The sound from a well-played violin is oscillation energy traveling through the air, but is hopefully not an annoyance. However, if a sound is unwelcome, we refer to it as noise. People can hear sounds between 20 Hz and 20,000 Hz. However, most noise concerns are typically below 4000 Hz.
Noise and vibration have several aspects that can be quantified: the frequency content, the amplitude of each frequency, and the relationship between the various frequencies, known as phase.
If a sound or vibration is composed of two or more frequencies where one is an integer multiple of the other, it is called a harmonic. Harmonic sounds are perceived to be more pleasant than non-harmonic sounds. Non-harmonic sounds are sometimes referred to as being harsh. Harshness refers to the quality of the sound or vibration rather than just the frequency or amplitude.
One acronym used to describe these types of phenomena is NVH, which stands for Noise, Vibration and Harshness. The term NVH is used mostly within the automotive industry, but can be applied across all industries.
NVH is a field of engineering which refers to the measurement, root cause understanding and mitigation of unwanted sound and vibration and reducing harshness. Some aspects of NVH engineering will be discussed in future articles.
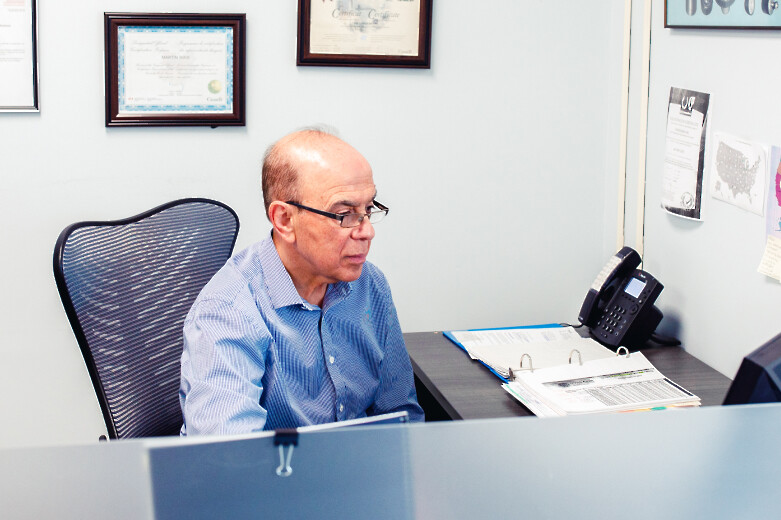
TRANE Chiller Mount Study
Vibration Isolation of the Chiller - Isolator Study.
Machine isolation is an important consideration in the installation of machine equipment, such as HVAC Chiller systems, that incorporate rotating components. These rotating components can produce excitations that can affect the function and durability of the system as well as the comfort of the building occupants and even the perceived quality of the brand. Machine isolation must be designed as a compromise between isolation and control. An isolation system with very little stiffness will provide significant isolation, but without displacement control, this system may experience excessive stresses during external loads such as wind loads or during foundation movements (such as during an earthquake or simply building swaying in the wind.)
Additionally, the system may experience excessive motion as the excitation from the rotating components aligns with resonance during start up and shut down events. Alternatively, a system that is very stiff will provide significant displacement control, but will transmit too much vibration into the surrounding environment. These vibrations may affect the customer comfort as well as building integrity and the perceived quality of the system. The purpose of adding isolators to the system is to reduce these vibrations into building. Ideally, a mount system should be designed such that the resonance of the chiller on its isolators occurs well below the minimum operating speed in a variable speed system while still maintaining enough control to minimize the effects of externally applied forces. Additionally, isolator choice also influences other characteristics such as installed height. A theoretical isolator can be described as a simple point stiffness, and can have almost any configuration. However, an actual isolator must be constructed of physical hardware that occupies real space and must be designed to survive the expected stresses experienced during its operational life cycle. This study is comparing 2 different mount systems under consideration for a Trane Chiller system. System A consists of 8 VibraSystems SRMT mounts with a loaded compression of 3” while System B consists of 8 VibraSystems SRMT vibration isolation mounts with a loaded compression of 2”.
The Mounts in System A must be physically larger than in System B to achieve the desired deflection.
System Isolators |
A |
B |
Unloaded Height |
16” |
8” |
Installed Deflection |
3” |
2” |
Installed Height |
13” |
6” |
This difference in Mount height will result in a difference in the installed system height.
Now we must determine how each system reacts to an external load applied to the system, First, calculate the Center of Pressure from a wind blowing on the side of the chiller.
Add Resulting Force position to mount height for each system to determine the moment arm from the force to ground. From these forces and moment arms, we can calculate the torque applied to the system.
Torque is equal to Force times Moment Arm. Therefore, the increased moment arm in System A causes the torque in System A to be 11% higher than the torque in System B.
Furthermore, the system stiffness is also influenced by the height of the mount system. This stiffness difference is coupled with the torque difference such that the displacement at the center of the chiller is 21% higher than the displacement at the center of the chiller in system B.
Conclusions:
Both Systems A and B should provide significant isolation for the rotating components in the chiller. A more detailed study can more accurately identify the expected isolation from each mount system. However, a study like that would require detailed mass and inertia data as well as a more accurate representation of the excitation frequencies.
However, System B should also provide isolation that is more than adequate as well as more lateral control of the Chiller in response to lateral wind forces or building movement.
VibraSystems recommends System B, the 2” precompression mounts.